Business Continuity Program
We Never Stop Logistics!
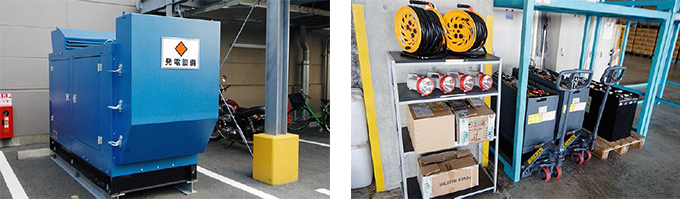
- KRT never stops Temperature Control of Warehouse!
- KRT never stops Order Processing!
- KRT always try to prepare for unexpected natural disasters!
Importance of Business Continuity Program (BCP) has been increased after the Great East Japan Earthquake and resulting Fukushima Daiichi Nuclear Power Plant Problem occurred on March 11, 2011.
Diesel Powered Generators
KRT has been actively working on Business Continuity Program (BCP) with an important mission of "Never stop the shipment of our clients as a reliable 3PL (Third-party Logistics) service provider”.
KRT installed diesel powered generators to warehouses shortly after the earthquake as part of the Business Continuity Program (BCP).
Data Centers
KRT protect your shipping records securely by establishing Okinawa and Saitama Data Centers!
IT system support is an essential for Business Continuity Program (BCP) .
KRT utilizes two data centers in Okinawa and Saitama prefectures to minimize the risk of earthquakes and brownouts.
Okinawa is far enough from Tokyo to avoid risk of damages from concurrent natural disasters.
Saitama Data Center was established to back up our system resilient enough to cope with an emergency situation anytime.
Battery Power Backup
(Utilization of Fork Truck Batteries for Power Source Backup)
Inexpensive and Convenient Idea!
KRT installed the power source backup system to keep the business machines (PC, multifunction printers/copiers, and electric order processing system) operating by utilizing batteries of folk trucks as part of the Business Continuity Program (BCP).
A unique but an easy installation idea for most public warehousing companies.
Order processing is an important function we must keep operating to avoid any delay of shipments.
Solar Power Generation/Storage System
Meaningless to just sell generated power!
Gift from the Sun & Eco Friendly Idea!
KRT focused on the solar power generation and installed the 481 of solar panels on the rooftop of Sakado Distribution Center as part of the Business Continuity Program (BCP).
Surprisingly, the power generated by solar panels can provide enough power to supply an office for day and night. Surplus electricity has been stored to 30 fork trucks batteries to supply electricity used in the evening, thus we do not sell our electricity to power company.
Our unique project was introduced on the blog by Optimal Power Solutions in Australia.
KRT achieved both Business Continuity Program (BCP) and Reduction of Carbon Dioxide (CO2) Emissions!.
Frequent Evacuation Drills
Japan is well-known as the land of earthquakes and tsunami.
For this reason, disaster and evacuation drills are usually held once or twice a year in schools and offices in Japan.
KRT has been conducting the evacuation drills for 6 times a year in each warehouse. Participation of all employees including part-time workers to be prepared for emergency has become regular practices for us.
QC
QC Circle Activities
KRT makes efforts to improve quality of our logistics services through QC circle activities.
QC circle activity is one of major reasons Japanese manufacturers successfully advanced global.
KRT started QC circle activities in 1998.
Kaizen at warehouse/dispatching office level enables day-to-day storage and transportation services more reliable.
Suggestion System
KRT enhances competitive advantages of clients by suggestion system.
KRT started suggestion system in 2010 which is inseparable with QC circle activities.
It aims to improve the issues and challenges encountered at day-to-day works.
Purpose of Suggestion System
Human Resources Development|Make Organization Active|Profit Improvement

Logistics Quality Improvement!
Customer Satisfaction Improvement!
Merits Achieved by QC Circle Activities
- Quality Improvement and Enhanced Customer Satisfaction
- Eliminating Waste and Loss Thoroughly
- Just In Time Delivery (Shorter Lead Time)
- Productivity Improvement and Production/transportation/storage Capacity Expansion
- Safety and Health
- Energy Saving and Be Green
- Increase of Communication Skills and Problem Solving Abilities
Productivity Improvement Committee
“To Achieve Lean Warehouse & Distribution Center”
KRT established “Productivity Improvement Committee” for the purpose of improving the operational efficiency and customer satisfaction at Kanto Warehouse and Sakado Distribution Center in February 2013.
Not satisfied with current condition, the committee identifies the inefficient labor deployment/idle time of each operation in order to improve the productivity per capita through enhanced QC circle activities.
Case Examples
- Waiting time reduction and streamlining of cargo handling operation by inbound truck reservation management system
- Optimizing the sortation work by the put-to-light system for piece picking operations
- Rationalization of warehousing operation (Loading/unloading)
- Improving order-picking efficiency